How Laser Cleaning Works: A Step-by-Step Guide to Efficient and Eco-Friendly Surface Cleaning
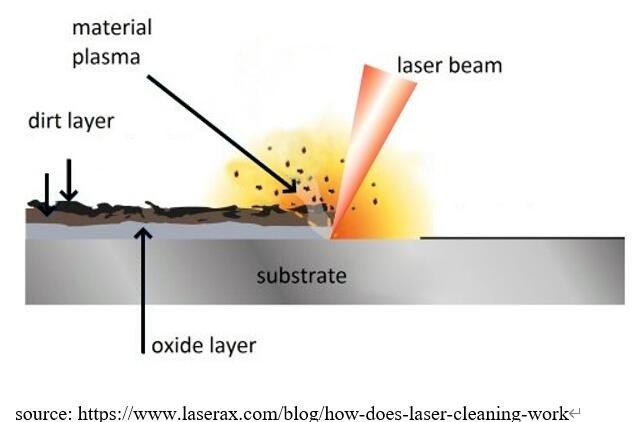
Laser cleaning is a revolutionary, eco-friendly process that efficiently removes rust, paint, oxides, and other contaminants from metal surfaces. It’s increasingly popular across various industries due to its precision and ability to clean without damaging the underlying material. In this guide, we’ll explore the five key steps in the laser cleaning process and why it’s becoming the preferred choice for industries.
- Understanding the Ablation Threshold
Laser cleaning relies on a principle called laser ablation, which uses high-energy laser beams to break down and remove surface layers. Each material has a unique ablation threshold—the minimum energy required to remove a layer.
When the laser beam strikes the material’s surface, the contaminant layer (like rust or paint) absorbs the energy, which breaks the molecular bonds, causing the layer to vaporize. The process only works if the laser’s energy is above the threshold for that specific material, ensuring precision cleaning.
- Selective Removal of Contaminants
It is highly selective, enabling it to remove one layer without affecting others. Imagine you have two layers on a surface—like rust on steel. The rust has a lower ablation threshold than the steel, allowing the laser to vaporize the rust layer while leaving the steel untouched.
This precision is especially useful when working on materials like aluminum or steel, where the contaminant layer (rust, oil, or paint) can be removed without damaging the base metal.
- Fast and Effective Cleaning with Pulsed Power
Laser cleaning systems offer two modes: continuous and pulsed. While continuous beams have their uses, pulsed lasers are generally more efficient for surface cleaning. Pulsing the laser increases the power over a shorter duration, similar to using a bigger hammer for faster impact.
This method speeds up the cleaning process while preventing the base material from overheating. Pulsed lasers allow for precise, high-speed cleaning, making them ideal for industrial applications requiring rapid contaminant removal.
- An Eco-Friendly, Consumable-Free Solution
Unlike traditional methods that require consumables like sand or chemical solvents, laser cleaning is completely consumable-free. It only needs electricity to function, which translates into lower operational costs and environmental impact.
Moreover, laser cleaning produces no chemical waste. This not only makes it safer for employees (no need for harsh chemicals or personal protective equipment) but also ensures compliance with environmental standards.
- Versatile Applications Across Industries
Laser cleaning’s versatility has opened doors for its use in many industrial applications, from removing rubber residue from tire molds to cleaning pipelines and preparing welding surfaces. Some of its most common applications include:
Pre-welding treatments to remove rust and contaminants
Post-welding treatments to remove oxides from stainless steel
Surface preparation to improve paint adhesion
Oxide removal on specialty alloys
Paint removal on damaged parts or production lines
Thanks to its ability to selectively remove layers, laser cleaning is also ideal for projects involving complex surfaces or materials.
Laser cleaning is reshaping industrial cleaning practices by offering an efficient, eco-friendly, and cost-effective alternative to traditional methods. By targeting specific layers with precision, it ensures thorough cleaning without harming the base material. If you’re interested in learning more about how laser cleaning could benefit your industry, consult a laser cleaning expert to explore the right solution for your needs.
For further guidance, contact Renovate Rx to discover our customizable workstations, production line solutions, and OEM laser systems tailored to your cleaning requirements.